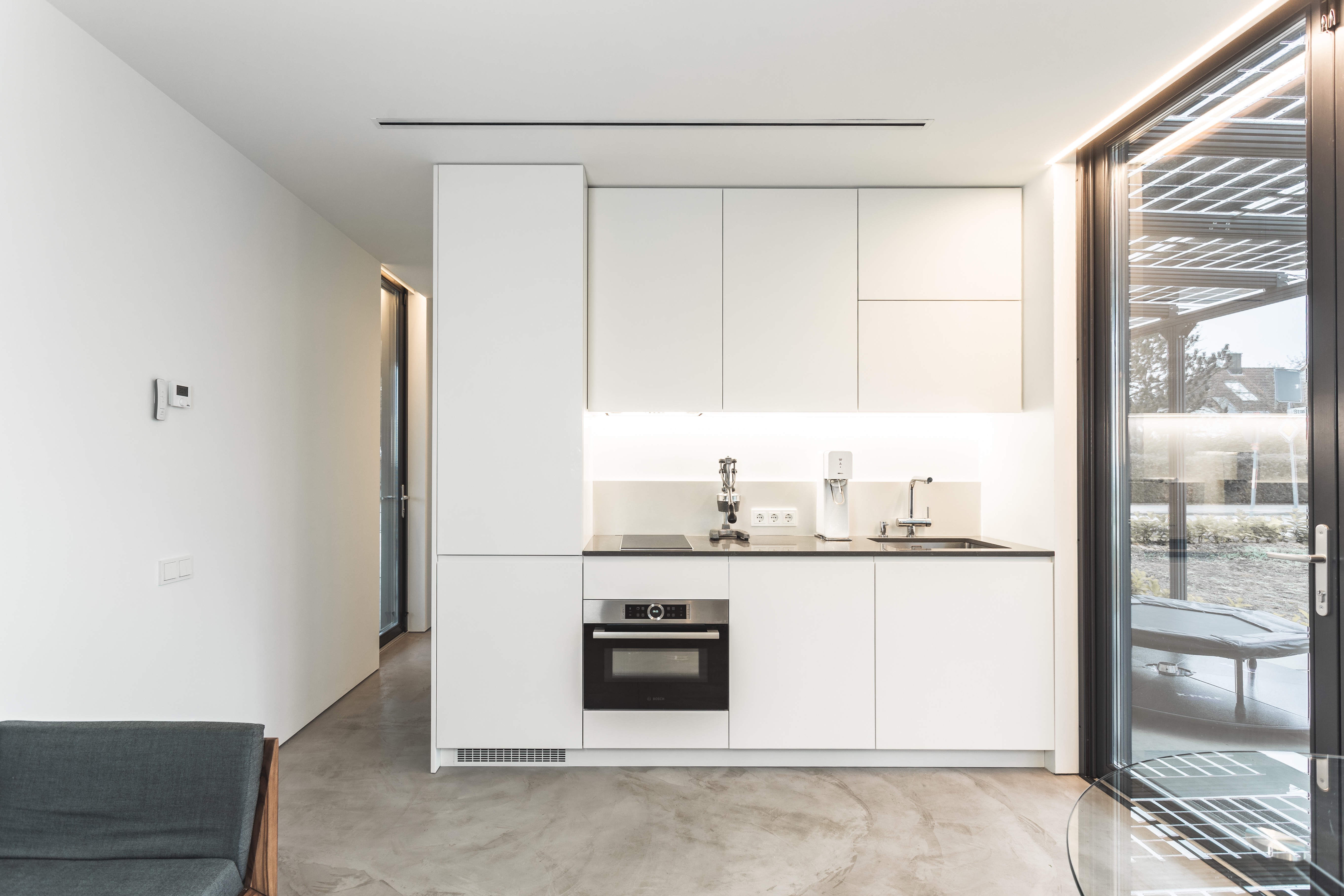
Our timber houses are affordable thanks to full prefabrication
Standardization and full prefabrication in the construction industry lead to more efficient planning, cost savings and improved working conditions. These methods enable precise, high-quality components and reduce complexity and material costs. The assembly of prefabricated modules speeds up the construction process and reduces labor costs, while innovative foundation techniques provide further savings. Overall, these approaches can reduce construction costs by up to 20% and support more sustainable, energy-efficient construction methods.
Analysis of cost reduction through standardization and full prefabrication in construction
The construction industry is faced with the challenge of maximizing efficiency and cost savings while maintaining quality standards. Two approaches that are promising in this regard are standardization and full prefabrication. These methods offer a number of advantages that affect both construction costs and the overall efficiency of the construction process. A detailed analysis of these approaches is carried out below.
1. Standardization in construction
Standardization in construction refers to the standardization of components and processes. This standardization results in more efficient planning, as the number of variables and thus the complexity of the planning process is reduced.
Another aspect of standardization is predictability in material orders. The ability to order larger quantities of standardized materials results in cost savings through economies of scale.
In addition, standardization enables an optimized integration of components such as insulation, heating systems and systems for energy generation and storage, such as photovoltaics and batteries, which leads to improved energy efficiency and a reduction in operating costs.
2. Advantages of factory manufacturing
Manufacturing components in a controlled factory environment offers several advantages. On the one hand, it enables more precise and efficient resource planning. The storage and retrieval of materials are simplified, which optimizes logistical processes.
Full prefabrication in factories enables high precision in the manufacture of components. This results in an increased quality of the end products, as with the support of mechanical manufacturing processes, a consistently high level of accuracy and processing quality can be guaranteed, which is difficult to achieve manually and on the construction site.
Another important aspect is the improvement of working conditions, which leads to lower illness rates and increased employee motivation. The controlled environment also allows experienced workers to be involved for a longer period of time.
3. Increasing efficiency through on-site assembly
The use of prefabricated modules significantly reduces the workload on the construction site. The main task is limited to assembling these modules and completing the connection work. This process requires fewer workers and results in a reduction in labor costs.
4. Foundation innovations
The integration of the base plate into prefabricated modules eliminates the need for a continuous base plate and enables the use of point foundations. This technique results in a significant reduction in material and labor costs in the area of foundation construction.
In summary, it can be stated that standardization and full prefabrication can lead to a significant cost reduction in construction. The reduction of planning and material costs, the optimization of working conditions and the simplification of construction site processes contribute to an increase in efficiency, which can result in a cost reduction of up to 20% compared to traditional, individually planned buildings.
These methods therefore not only offer economic benefits, but also support the trend towards more sustainable and energy-efficient construction methods.